One of the key methods to prevent Printed Circuit Board (PCB) defects is by managing the environmental conditions within the factory.
Without proper control of humidity and temperature on the manufacturing floor, expensive components—and potentially entire assemblies—can be compromised, leading to quality issues and additional costs.
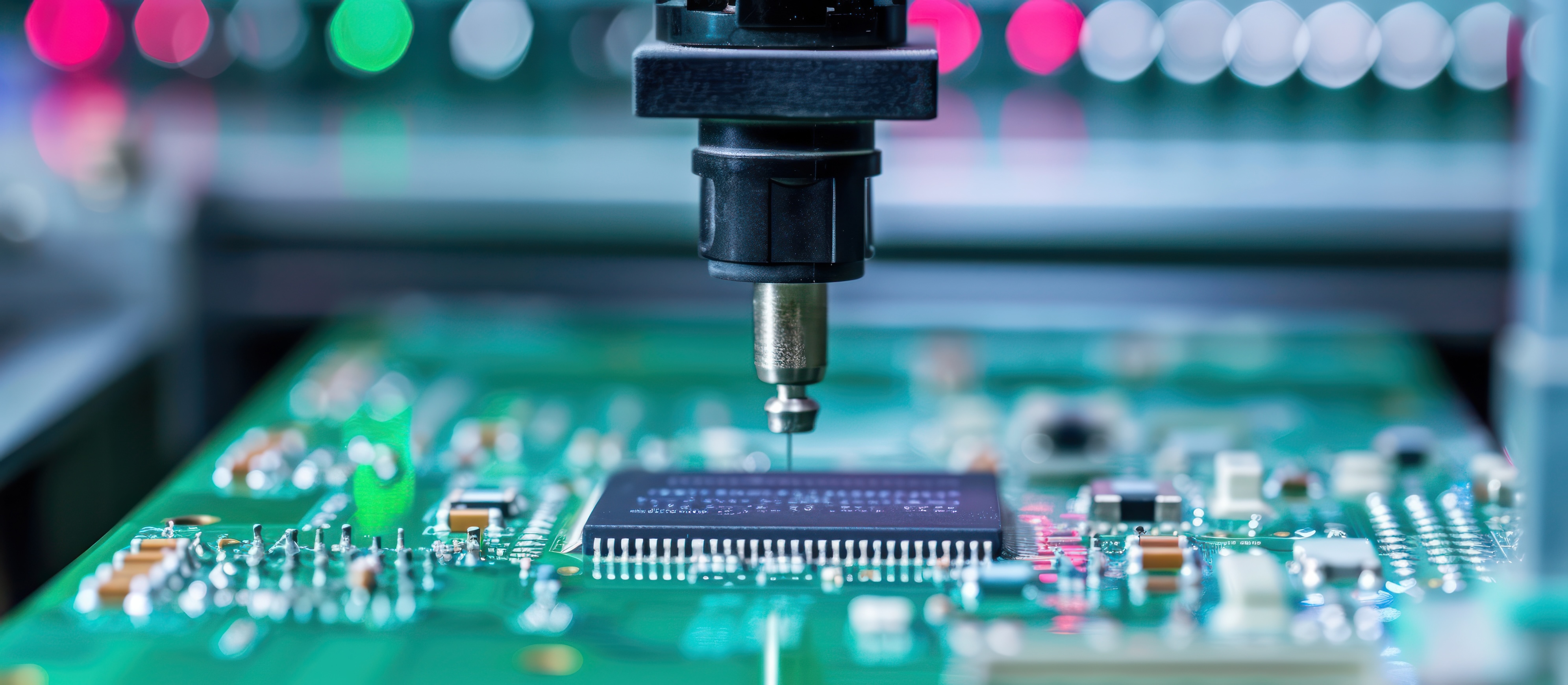
Humidity monitoring
High levels of humidity in a manufacturing environment can lead to serious issues such as slumping, where solder paste absorbs too much water and causes bridging during reflow, and solderballing (or “popcorning”), resulting from excessive water absorption and poor coalescence.
Out-gassing can also occur, where water creeps under surface mounts, especially BGAs, causing pressure build-up that can blow off covers.
Conversely, low humidity causes flux to evaporate too quickly, drying out solder paste and leading to poor release from stencils and insufficient solder joint defects.
Temperature monitoring
High temperatures in a manufacturing environment decrease solder paste viscosity, leading to issues such as paste smearing and slumping, which can cause bridging and solderballing defects like voiding.
Additionally, elevated temperatures may increase solder oxidation, compromising solderability.
Low temperatures can increase solder paste viscosity, resulting in poor printing behavior, such as inadequate release and rolling, and print voiding, where the paste becomes too solid to print correctly.
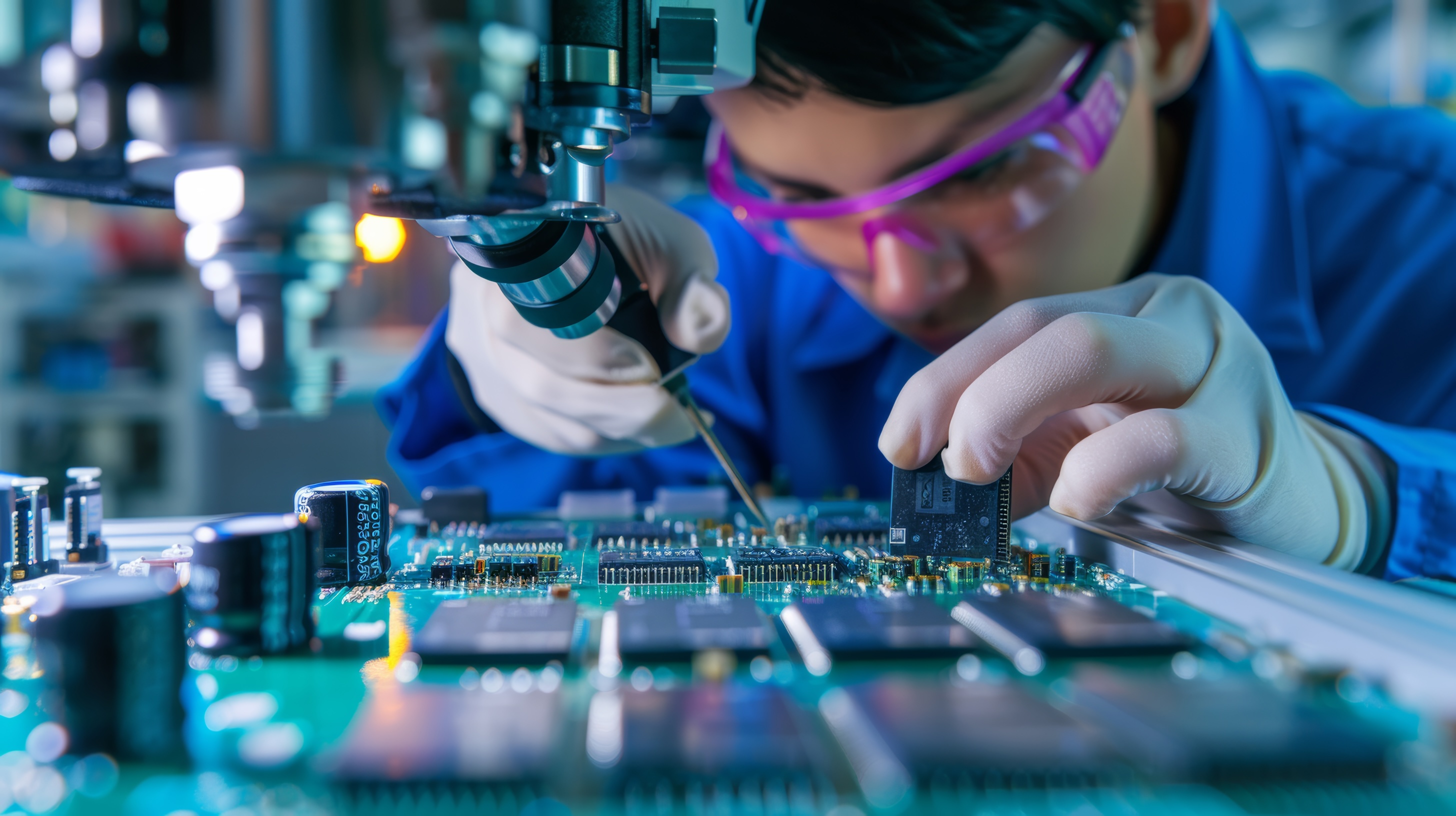
Recommended range and conditions
When it comes to maintaining optimal environmental conditions in SMT lines, expert opinions on relative humidity (Rh) and temperature ranges can vary. Some experts recommend broader ranges, such as 35-65%, 40-70%, or 20-50%, while others suggest maintaining Rh around 60% to prevent defects and lifecycle issues. Ultimately, the ideal Rh range often depends on the specific requirements and preferences of your products and processes.
Similarly, while there is less variation in expert opinions regarding temperature, the general consensus is that solder paste performs best within the 68-78 degrees Fahrenheit range, which coincides with normal human comfort levels. However, it’s important to remember that different solder pastes can behave differently under various conditions, so allowing some flexibility based on the specific product is always advisable.
Fourtec solutions
Fourtec’s monitoring solutions (the MicroLog and MicroLite Temp & RH) provide real-time monitoring and control of temperature and humidity levels, ensuring that critical parameters are maintained within desired ranges. Fourtec’s data loggers are easy to install and operate and feature advanced data logging and reporting capabilities for enhanced analysis and decision-making.
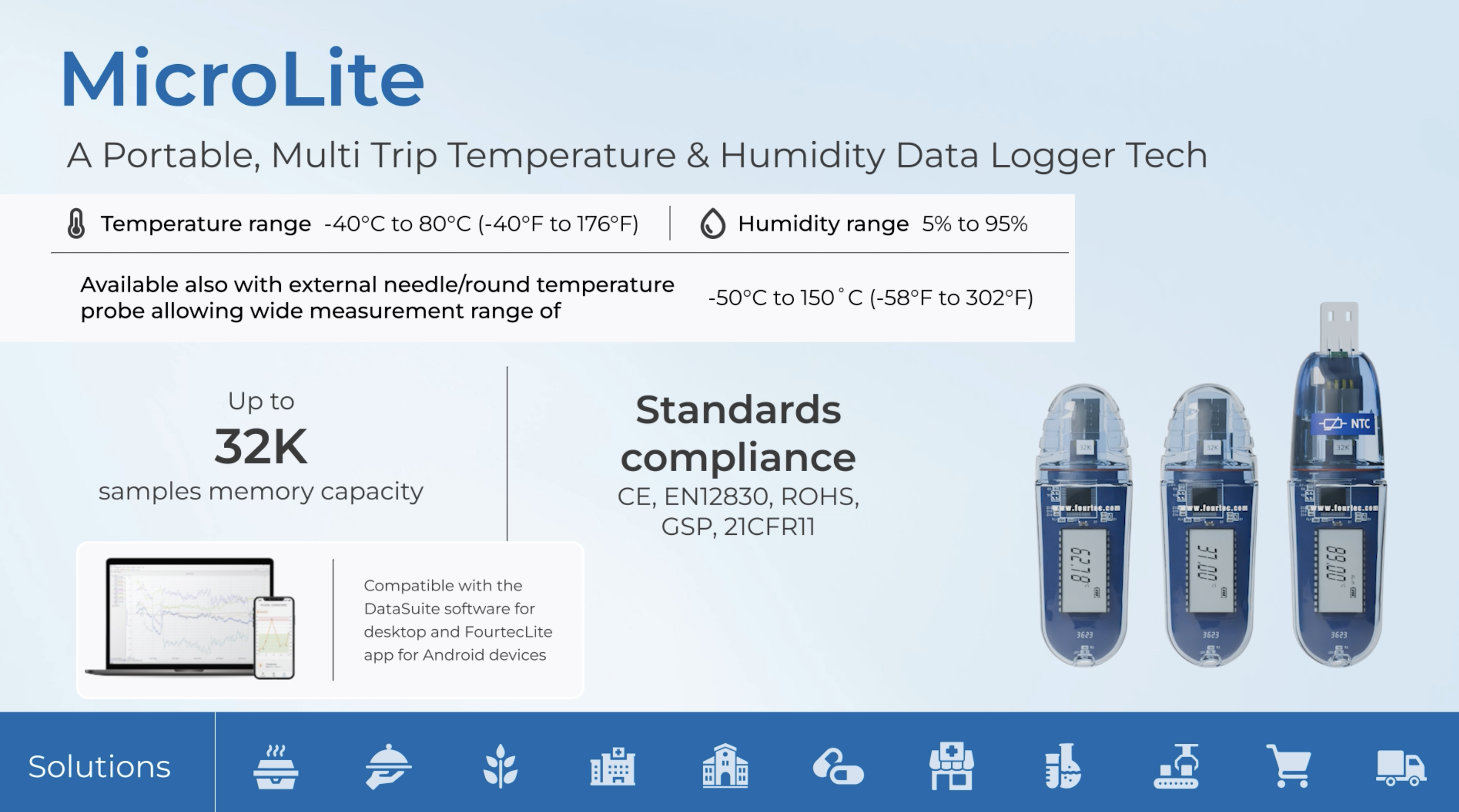
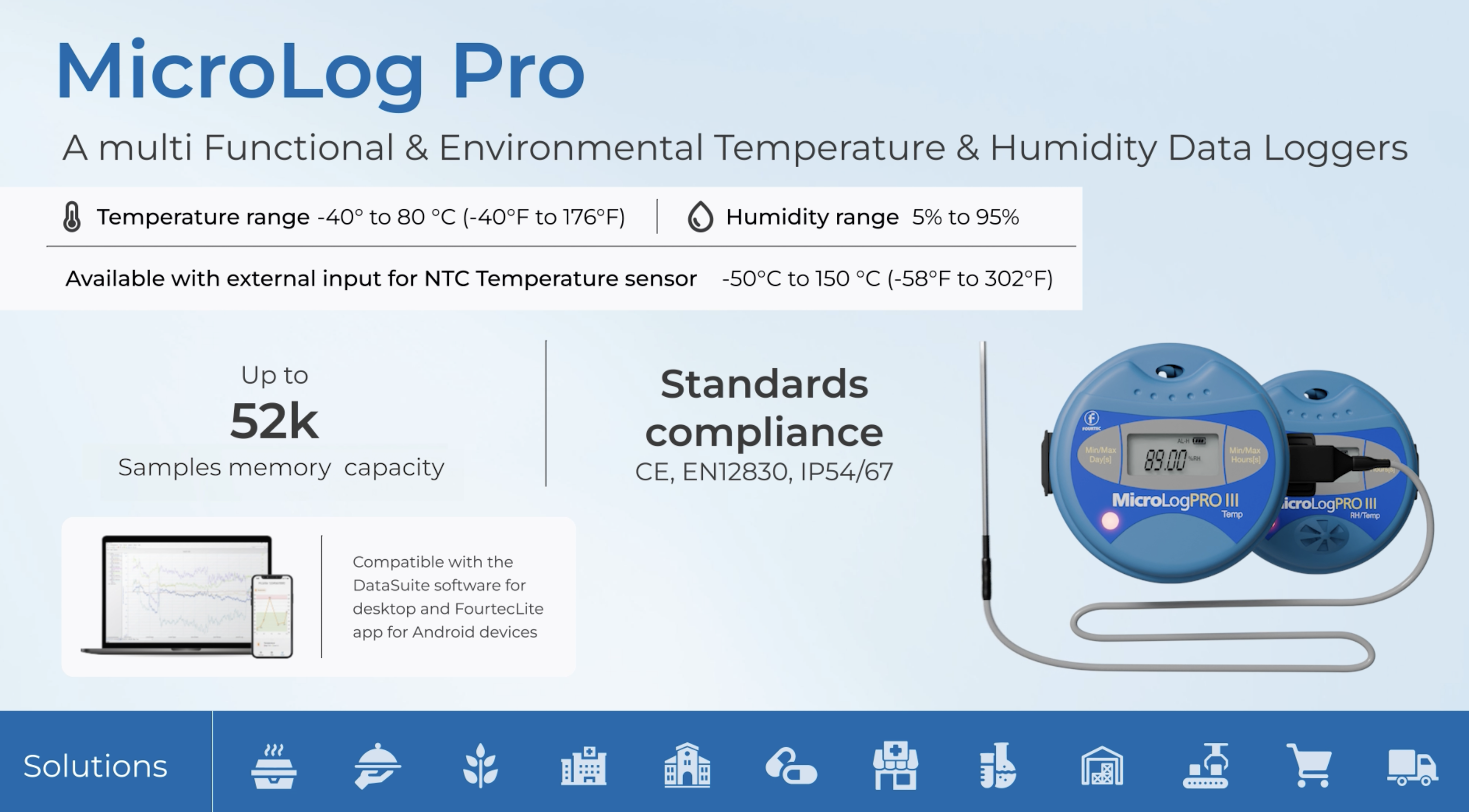